افزایش کیفیت جوش با شناخت بهترین الکترودها و مواد مصرفی
کیفیت جوش، ستون فقرات ایمنی و دوام سازههای صنعتی و عمرانی است. دستیابی به جوشی مستحکم و عاری از عیوب، تنها به مهارت جوشکار و تجهیزات پیشرفته محدود نمیشود، بلکه شناخت عمیق و انتخاب دقیق بهترین الکترود جوشکاری و مواد مصرفی جوشکاری نقشی کلیدی در افزایش چشمگیر کیفیت جوش ایفا میکند. این مواد، از آغاز فرآیند تا پایان آن، به طور مستقیم بر خواص مکانیکی، ظاهر و طول عمر اتصال تأثیر میگذارند. در حقیقت، هر گونه سهلانگاری در انتخاب یا نگهداری آنها میتواند به پیامدهای جبرانناپذیری در استحکام و پایداری سازه منجر شود. این راهنما از آلیاژ صنعت ایلیا به شما کمک میکند تا با اتخاذ تصمیماتی آگاهانه، فرآیند جوشکاری خود را بهینه کرده و به استانداردهای بالاتری از کیفیت دست یابید.
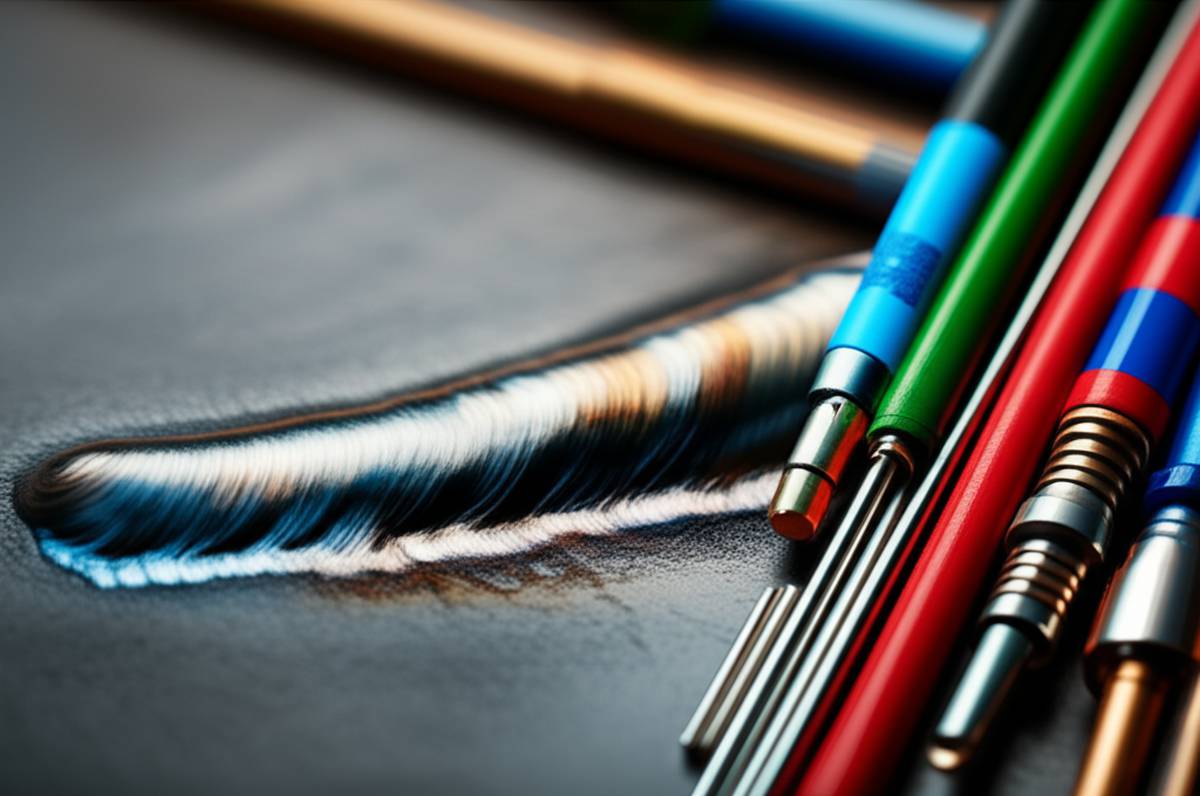
درک مبانی کیفیت جوش و عوامل مؤثر بر آن
کیفیت جوش فراتر از یک ظاهر صاف و بدون پاشش است؛ این مفهوم شامل مجموعهای از خواص مکانیکی و فیزیکی است که تضمینکننده عملکرد مطلوب اتصال در طول عمر مفید آن است. استحکام کششی، مقاومت به ضربه، نفوذ کافی، عدم وجود تخلخل، ترک و ناخالصیها از جمله شاخصهای اصلی کیفیت جوش به شمار میروند. یک جوش باکیفیت باید بتواند بارهای طراحی شده را تحمل کند، در برابر عوامل محیطی مقاوم باشد و از نظر بصری نیز قابل قبول باشد.
عوامل متعددی بر دستیابی به این سطح از کیفیت تأثیر میگذارند. مهارت جوشکار، تنظیمات صحیح دستگاه جوش (شامل جریان، ولتاژ و سرعت پیشروی)، آمادهسازی مناسب قطعه کار (مانند تمیزکاری و پیشگرمایش) و محیط جوشکاری (مانند دما و رطوبت) همگی از اهمیت بالایی برخوردارند. اما در این میان، انتخاب و استفاده صحیح از مواد مصرفی جوشکاری، نقش تعیینکنندهای دارد. مواد مصرفی نامناسب میتوانند حتی با وجود مهارت بالای جوشکار و تجهیزات پیشرفته، منجر به بروز عیوب رایج جوش شوند و کیفیت نهایی را به شدت کاهش دهند.
انتخاب “بهترین” مواد مصرفی، کلید دستیابی به کیفیت بالاست، زیرا این مواد مستقیماً بر خواص مکانیکی و ظاهری جوش تأثیر میگذارند. به عنوان مثال، الکترودی که ترکیب شیمیایی آن با فلز پایه همخوانی نداشته باشد، میتواند منجر به تشکیل فازهای نامطلوب در جوش و کاهش استحکام آن شود. همچنین، گاز محافظ نامناسب میتواند باعث آلودگی حوضچه مذاب و ایجاد تخلخل در جوش شود. بنابراین، شناخت دقیق این مواد و نحوه انتخاب آنها، گامی اساسی در جهت افزایش کیفیت جوش و کاهش ضایعات است.
شناخت بهترین الکترودها برای افزایش کیفیت جوش
الکترود در فرآیند جوشکاری نه تنها وظیفه ایجاد و حفظ قوس الکتریکی را بر عهده دارد، بلکه با ذوب شدن خود، فلز پرکننده لازم برای ایجاد اتصال را تأمین میکند. همچنین، روپوش یا فلاکس آن نقش حیاتی در محافظت از حوضچه مذاب در برابر آلودگیهای اتمسفری و بهبود خواص مکانیکی جوش نهایی دارد. در واقع، کیفیت و نوع الکترود، تعیینکننده بسیاری از ویژگیهای جوش نهایی از جمله استحکام، مقاومت به خوردگی، ظاهر و نفوذ خواهد بود.
الکترودهای روپوشدار (SMAW/جوشکاری با قوس دستی)
این نوع الکترودها که در جوشکاری با قوس دستی (SMAW) کاربرد فراوان دارند، شامل یک هسته فلزی و پوششی از مواد شیمیایی به نام فلاکس هستند. فلاکس در حین جوشکاری ذوب شده و گازها و سربارهای تولید میکند که از حوضچه مذاب در برابر اکسیژن و نیتروژن هوا محافظت میکنند. درک تأثیر هر نوع الکترود بر کیفیت جوش برای انتخاب صحیح ضروری است:
- E6010: این الکترود دارای نفوذ عمیق و قوس قوی است که برای جوشکاری ریشه و درزهای تنگ بسیار مناسب است. ظاهر مهره جوش آن کمی خشن است، اما استحکام و نفوذ عالی را فراهم میکند و به همین دلیل برای لولهکشی و ساخت و سازهای سنگین کاربرد دارد.
- E6011: مشابه E6010 است، اما میتواند با جریان متناوب (AC) نیز کار کند. این الکترود نیز نفوذ بالایی دارد و برای جوشکاری فلزات زنگزده یا کثیف مفید است، اما ظاهر جوش آن نیز ممکن است کمی نامنظم باشد.
- E6013: این الکترود برای جوشکاری با جریانهای AC و DC مناسب است و قوسی آرام و پایدار دارد. سرباره آن به راحتی جدا میشود و ظاهر مهره جوش بسیار صاف و زیباست. نفوذ آن متوسط است و برای کارهای عمومی، جوشکاری ورقهای نازک و کاربردهایی که ظاهر جوش اهمیت دارد، بهترین الکترود جوشکاری محسوب میشود.
- E7018: این الکترود قلیایی (کم هیدروژن) است و برای دستیابی به جوشهایی با استحکام بالا، مقاومت عالی به ضربه و تخلخل بسیار کم استفاده میشود. حساسیت کمی به ترکیدگی دارد و برای جوشکاری فولادهای پرکربن و سازههای تحت بار دینامیکی ایدهآل است. برای حفظ کیفیت، باید قبل از استفاده پیشگرمایش و در کوره خشک نگهداری شود.
- E7024: یک الکترود با سرعت رسوبدهی بالا و سرباره سنگین که برای جوشکاری در موقعیتهای تخت و افقی بسیار مناسب است. قوسی نرم و پایدار دارد و ظاهر جوش بسیار صاف و زیبا با نفوذ متوسط تا زیاد ایجاد میکند. برای افزایش بهرهوری در جوشکاری قطعات ضخیم کاربرد دارد.
سیم جوش (GMAW/MIG و FCAW)
در فرآیندهای جوشکاری میگ (MIG) و افسیایدبلیو (FCAW)، سیم جوش به عنوان فلز پرکننده پیوسته عمل میکند. انتخاب سیم جوش مناسب برای دستیابی به بهترین کیفیت جوش، حیاتی است:
- سیمهای جامد (MIG): این سیمها نیاز به گاز محافظ خارجی (مانند آرگون، CO2 یا مخلوط آنها) دارند. سرعت جوشکاری با آنها بالاست، پاشش کمتری دارند و جوشهایی با ظاهر تمیز و خواص مکانیکی خوب تولید میکنند. انتخاب نوع سیم جامد (مانند ER70S-6 برای فولاد کربن) بستگی به نوع فلز پایه و خواص مورد نظر دارد.
- سیمهای توپودری (FCAW): این سیمها دارای فلاکس داخلی هستند که محافظت از حوضچه مذاب را بر عهده میگیرد. برخی از آنها نیاز به گاز محافظ ندارند (خود محافظ) و برخی دیگر نیاز به گاز محافظ خارجی دارند. سیمهای توپودری سرعت رسوبدهی بالا و نفوذ خوبی دارند و برای جوشکاری در فضای باز یا روی فلزات نسبتاً کثیف مناسباند، اما پاشش آنها ممکن است بیشتر باشد.
تنگستن (GTAW/TIG)
در جوشکاری تیگ (TIG)، الکترود تنگستن غیرمصرفی است و تنها برای ایجاد و حفظ قوس الکتریکی به کار میرود. پایداری قوس و عدم آلودگی حوضچه مذاب به واسطه انتخاب تنگستن مناسب، در کیفیت جوش ظریف تیگ بسیار مؤثر است:
- تنگستن خالص (سبز): برای جوشکاری AC (آلومینیوم و منیزیم) مناسب است و پایداری قوس خوبی دارد.
- تنگستن توریمدار (قرمز): بهترین الکترود جوشکاری برای DC (فولاد، استنلس استیل، مس) است و شروع قوس و پایداری عالی دارد، اما به دلیل رادیواکتیو بودن توریم، کمتر توصیه میشود.
- تنگستن لانتانیمدار (طلایی): جایگزین مناسبی برای توریمدار است، برای AC و DC کاربرد دارد و شروع قوس عالی و عمر طولانی دارد.
- تنگستن سریمدار (خاکستری): برای جریانهای پایین AC و DC مناسب است و شروع قوس خوبی را فراهم میکند.
ویژگیهای یک الکترود “خوب” برای کیفیت برتر
افزایش کیفیت جوش نیازمند شناخت دقیق ویژگیهای الکترود است. یک الکترود مناسب باید چندین ویژگی کلیدی داشته باشد تا عملکرد مطلوب را ارائه دهد:
- پایداری قوس: قوسی پایدار و بدون نوسان، نشاندهنده فرآیندی با ثبات است که از بروز عیوبی مانند تخلخل و ناهمواری جلوگیری میکند. الکترودهای با کیفیت، قوسی یکنواخت و قابل کنترل ایجاد میکنند.
- رسانایی الکتریکی بالا: این ویژگی باعث کاهش مقاومت الکتریکی و گرمایش بهینه در نوک الکترود میشود که به نوبه خود منجر به ذوب یکنواخت و نفوذ مطلوب میگردد.
- ترکیب شیمیایی مناسب: فلز پرکننده الکترود باید با فلز پایه سازگار باشد تا خواص مکانیکی مورد نظر (مانند استحکام کششی، مقاومت به ضربه و سختی) در جوش نهایی حاصل شود. این مورد در انتخاب الکترود مناسب برای کیفیت جوش بسیار حیاتی است.
- مقاومت در برابر رطوبت و خوردگی: به خصوص در الکترودهای کم هیدروژن مانند E7018، مقاومت به رطوبت برای جلوگیری از جذب هیدروژن و بروز ترکیدگی ناشی از هیدروژن اهمیت حیاتی دارد. نگهداری صحیح مواد مصرفی جوشکاری در محیط خشک و بدون رطوبت از اهمیت بسزایی برخوردار است.
- قابلیت نفوذ و ذوبپذیری: الکترود باید به گونهای باشد که بتواند عمق نفوذ مطلوب را در فلز پایه ایجاد کند و همزمان، ذوب پایداری داشته باشد تا حوضچه مذاب به خوبی کنترل شود و به بهبود ظاهر جوش کمک کند.
- شکلپذیری و ظاهر مهره جوش: در بسیاری از کاربردها، ظاهر مهره جوش نیز اهمیت دارد. الکترودهایی که سربارهای راحت جداشونده و مهره جوشی صاف و یکنواخت تولید میکنند، در ارزیابی بصری امتیاز بالاتری میگیرند.
انتخاب الکترود مناسب، نه تنها به نوع فلز و فرآیند جوشکاری، بلکه به خواص مکانیکی مورد انتظار و شرایط محیطی نیز بستگی دارد. مشاوره با متخصصین و تامینکنندگان معتبر مانند آلیاژ صنعت ایلیا میتواند در این انتخاب حیاتی، راهگشا باشد.
مواد مصرفی مکمل و نقش آنها در افزایش کیفیت جوش
علاوه بر الکترود و سیم جوش، سایر مواد مصرفی نیز نقشی حیاتی در تضمین کیفیت و پایداری فرآیند جوشکاری دارند. گازهای محافظ و فلاکسها از جمله این مواد هستند که هر یک وظایف ویژهای را در محیط جوشکاری بر عهده دارند.
گازهای محافظ
گاز محافظ وظیفه دارد تا حوضچه مذاب، نوک الکترود یا سیم جوش و ناحیه اطراف جوش را از تماس با گازهای مضر اتمسفر مانند اکسیژن و نیتروژن حفظ کند. این گازها از اکسیداسیون، ایجاد تخلخل و سایر آلودگیها جلوگیری کرده و پایداری قوس را نیز بهبود میبخشند. انتخاب گاز محافظ مناسب برای جوشکاری در فرآیندهای GMAW (MIG) و GTAW (TIG) بسیار مهم است:
- آرگون (Ar): رایجترین گاز محافظ برای جوشکاری TIG و MIG آلومینیوم، منیزیم، مس، نیکل و فولادهای ضد زنگ. قوسی پایدار و کنترلپذیر ایجاد میکند و منجر به ظاهری تمیز و بدون پاشش میشود.
- دی اکسید کربن (CO2): یک گاز فعال که در جوشکاری MIG فولاد کربن و برخی فولادهای کمآلیاژ استفاده میشود. نفوذ عمیقی ایجاد میکند و ارزانتر است، اما ممکن است پاشش بیشتری داشته باشد.
- مخلوط آرگون و CO2: این مخلوطها (مثلاً ۸۰% آرگون + ۲۰% CO2) برای جوشکاری MIG فولاد کربن و استنلس استیل بسیار محبوب هستند. ترکیب مزایای هر دو گاز، یعنی پایداری قوس آرگون و نفوذ CO2 را فراهم میکنند و منجر به کاهش پاشش و بهبود ظاهر جوش میشوند.
- هلیوم (He): به دلیل رسانایی حرارتی بالا، قوسی داغتر ایجاد میکند که برای جوشکاری فلزات ضخیمتر یا فلزاتی با رسانایی حرارتی بالا مانند مس و آلومینیوم مفید است. اغلب به صورت مخلوط با آرگون استفاده میشود.
فلاکسها (Fluxes)
فلاکسها موادی هستند که در الکترودهای روپوشدار (SMAW)، سیمهای توپودری (FCAW) و در جوشکاری زیرپودری (SAW) به کار میروند. نقش فلاکسها فراتر از محافظت از حوضچه مذاب است؛ آنها میتوانند:
- سطح فلز پایه را تمیز کنند: با واکنش با ناخالصیها، آنها را به سرباره منتقل میکنند.
- خواص مکانیکی را بهبود بخشند: با افزودن عناصر آلیاژی به فلز جوش، خواص آن را تنظیم میکنند.
- پایداری قوس را افزایش دهند: با تولید گازهای یونیزه کننده، به پایداری قوس کمک میکنند.
- شکل مهره جوش را تنظیم کنند: با کنترل سیالیت حوضچه مذاب و ویژگیهای سرباره، به ظاهر و شکل مهره جوش کمک میکنند.
تاثیر فلاکس بر جلوگیری از عیوب (مانند ناخالصی، اکسیداسیون، و تخلخل) و بهبود ظاهر جوش بسیار قابل توجه است. سرباره حاصل از فلاکس پس از انجماد، روی سطح جوش را میپوشاند و پس از سرد شدن، به راحتی قابل جدا شدن است. فلاکسهای مختلف (اسیدی، بازی، خنثی) بسته به نوع فلز، فرآیند و خواص مورد انتظار جوش انتخاب میشوند.
انتخاب هوشمندانه الکترود و مواد مصرفی برای کیفیت بهینه: یک رویکرد سیستماتیک
برای دستیابی به افزایش کیفیت جوش و جوشکاری بدون عیب، انتخاب مواد مصرفی باید بر اساس یک رویکرد سیستماتیک و آگاهانه انجام شود. مراحل زیر به شما در این فرآیند کمک میکند:
- گام اول: شناخت فلز پایه و ضخامت آن:
اولین گام، شناخت دقیق فلز یا آلیاژی است که قرار است جوشکاری شود. نوع فلز (مانند فولاد کربن، استنلس استیل، آلومینیوم)، ترکیب شیمیایی آن و ضخامت قطعات، تعیینکننده اصلی در انتخاب الکترود و سیم جوش است. به عنوان مثال، برای جوشکاری آلومینیوم، الکترودهای آلومینیومی و گاز آرگون ضروری است، در حالی که برای فولادهای پرکربن ممکن است به الکترودهای کم هیدروژن و پیشگرمایش نیاز باشد.
- گام دوم: تعیین فرآیند جوشکاری:
هر فرآیند جوشکاری (SMAW, GMAW, GTAW, FCAW, SAW) نیازمندیهای خاص خود را از نظر مواد مصرفی دارد. سیم جوش برای MIG/MAG، الکترود روپوشدار برای قوس دستی، تنگستن برای TIG و فلاکس مخصوص برای SAW/FCAW مناسب است. انتخاب فرآیند، دامنه گزینههای مواد مصرفی را محدود میکند.
- گام سوم: مشخص کردن الزامات کیفیت و خواص مکانیکی مورد نظر:
چه خواصی از جوش نهایی انتظار میرود؟ استحکام کششی بالا؟ مقاومت به ضربه در دماهای پایین؟ مقاومت به خوردگی؟ سختی؟ این الزامات به طور مستقیم بر انتخاب نوع الکترود یا سیم جوش (از نظر ترکیب آلیاژی و خواص مکانیکی) تأثیر میگذارند. به عنوان مثال، برای سازههای تحت بارهای دینامیکی، افزایش استحکام جوش از اهمیت ویژهای برخوردار است.
- گام چهارم: در نظر گرفتن موقعیت جوشکاری و شرایط محیطی:
آیا جوشکاری در موقعیت تخت، افقی، عمودی یا سقفی انجام میشود؟ برخی الکترودها (مانند E6013) برای تمام موقعیتها مناسباند، در حالی که برخی دیگر (مانند E7024) عمدتاً برای موقعیتهای تخت به کار میروند. همچنین، شرایط محیطی مانند دما، رطوبت و تهویه نیز در انتخاب الکترود (مثلاً حساسیت به رطوبت E7018) و گاز محافظ (مثلاً استفاده در فضای باز) مهم هستند.
- گام پنجم: انتخاب قطر مناسب الکترود/سیم جوش:
اهمیت قطر الکترود در کیفیت جوش بسیار بالاست. قطر الکترود یا سیم جوش باید متناسب با ضخامت فلز پایه و جریان جوشکاری انتخاب شود. قطر نامناسب میتواند منجر به نفوذ ناکافی، ذوب نشدن کنارهها، سوختگی یا تغییر شکل بیش از حد شود. برای فلزات نازکتر، قطرهای کوچکتر و برای فلزات ضخیمتر، قطرهای بزرگتر به کار میروند تا بهترین نفوذ و کنترل حوضچه مذاب حاصل شود.
- گام ششم: توجه به استانداردها و گواهینامهها:
الکترودها و مواد مصرفی باید با استانداردهای بینالمللی مانند AWS (انجمن جوشکاری آمریکا) یا ISO (سازمان بینالمللی استانداردسازی) مطابقت داشته باشند. این استانداردها، تضمینکننده کیفیت، ترکیب شیمیایی و خواص مکانیکی مشخص شده برای مواد مصرفی هستند. استفاده از محصولات دارای گواهینامه معتبر، اطمینان از کیفیت و قابلیت ردیابی محصول را فراهم میکند.
- گام هفتم: بررسی مقرون به صرفه بودن و بهرهوری:
در حالی که کیفیت جوش اولویت اصلی است، هزینه و بهرهوری نیز باید در نظر گرفته شود. انتخاب مواد مصرفی با کیفیت بالا ممکن است در ابتدا گرانتر به نظر برسد، اما با کاهش ضایعات، دوبارهکاریها و افزایش طول عمر جوش، در بلندمدت مقرون به صرفه خواهد بود. همچنین، نرخ رسوبدهی مواد مصرفی بر بهرهوری کلی فرآیند تأثیر میگذارد.
در انتخاب مواد مصرفی، توجه به جزئیات فنی و مطابقت آنها با الزامات پروژه، تفاوت میان یک جوش معمولی و یک جوش با کیفیت عالی را رقم میزند.
نکات کلیدی برای حفظ کیفیت مواد مصرفی و جلوگیری از عیوب جوش
کیفیت مواد مصرفی تنها به انتخاب اولیه آنها محدود نمیشود؛ بلکه نحوه نگهداری و استفاده از آنها نیز تأثیر بسزایی در افزایش کیفیت جوش و جلوگیری از عیوب دارد. رعایت نکات زیر، تضمینکننده عملکرد بهینه و افزایش عمر مفید مواد مصرفی است:
- نگهداری و انبارداری صحیح الکترودها و سیم جوشها:
رطوبت، دشمن اصلی الکترودها، به خصوص انواع قلیایی (مانند E7018) است. جذب رطوبت میتواند منجر به افزایش هیدروژن در جوش و در نتیجه بروز ترکیدگی ناشی از هیدروژن شود. الکترودها باید در کوره خشککن نگهداری شوند یا قبل از استفاده، در دمای و زمان مشخصی پیشگرمایش شوند. سیم جوشها نیز باید در بستهبندی اصلی خود و در محیط خشک و بدون گرد و غبار نگهداری شوند تا از آلودگی، زنگزدگی و جذب رطوبت جلوگیری شود. این نگهداری صحیح مواد مصرفی جوشکاری، از روشهای تشخیص کیفیت الکترود در آینده نیز مهمتر است.
- پیشگرمایش الکترودها (در صورت لزوم):
برخی الکترودها (مانند E7018) نیاز به پیشگرمایش دارند تا رطوبت جذب شده از روکش آنها خارج شود. این کار به کاهش میزان هیدروژن در جوش و جلوگیری از ترکیدگی کمک میکند. دستورالعملهای سازنده الکترود برای دما و زمان پیشگرمایش باید به دقت رعایت شود.
- بازرسی بصری مواد مصرفی قبل از استفاده:
همیشه قبل از شروع جوشکاری، الکترودها و سیم جوشها را از نظر وجود آسیبدیدگی، زنگزدگی، تغییر رنگ یا آلودگی بررسی کنید. بستهبندیهای آسیبدیده یا الکترودهای مرطوب نباید مورد استفاده قرار گیرند. تاریخ انقضای سیم جوشها و الکترودها را نیز چک کنید.
- تأثیر کیفیت برق و تجهیزات بر عملکرد مواد مصرفی:
نوسانات ولتاژ و آمپر، یا نقص در سیستم تغذیه سیم در دستگاههای MIG/MAG، میتواند بر پایداری قوس و در نتیجه کیفیت جوش تأثیر منفی بگذارد. اطمینان از سلامت تجهیزات و کیفیت برق ورودی، مکمل استفاده از مواد مصرفی با کیفیت است.
- نقش مهارت جوشکار در استفاده بهینه از مواد مصرفی:
حتی بهترین مواد مصرفی نیز بدون مهارت کافی جوشکار، نمیتوانند کیفیت مطلوب را ارائه دهند. کنترل صحیح پارامترهای جوشکاری (جریان، ولتاژ، سرعت پیشروی، طول قوس)، زاویه الکترود و تکنیک مناسب، همگی برای بهرهبرداری کامل از پتانسیل مواد مصرفی ضروری هستند. آموزش و تجربه مستمر، عوامل کلیدی در کاهش عیوب جوش و افزایش استحکام جوش هستند.
رعایت این نکات به همراه انتخاب هوشمندانه، نه تنها به افزایش کیفیت جوش منجر میشود، بلکه به کاهش ضایعات، صرفهجویی در هزینهها و افزایش طول عمر سازهها نیز کمک شایانی میکند. شرکت آلیاژ صنعت ایلیا با ارائه مشاورههای تخصصی و تأمین مواد مصرفی جوشکاری باکیفیت و مطابق با استانداردهای روز دنیا، در کنار شماست تا پروژههایتان را با بالاترین کیفیت به انجام رسانید.
عیوب جوش و راههای پیشگیری با انتخاب مواد مصرفی:
- تخلخل: ناشی از حبس گازها در حوضچه مذاب. با استفاده از گاز محافظ مناسب (با خلوص بالا)، فلاکس فعال و نگهداری صحیح الکترودها (خشک نگه داشتن)، میتوان از آن جلوگیری کرد.
- ترکیدگی (Crack): میتواند ناشی از هیدروژن (در الکترودهای مرطوب)، تنشهای پسماند یا ترکیب شیمیایی نامناسب فلز جوش باشد. انتخاب الکترودهای کم هیدروژن (E7018) و پیشگرمایش مناسب، نقش مهمی در پیشگیری دارد.
- نفوذ ناکافی: زمانی که فلز جوش به اندازه کافی به عمق درز نفوذ نمیکند. انتخاب قطر مناسب الکترود، جریان و ولتاژ صحیح و تکنیک جوشکاری مناسب، نفوذ را بهبود میبخشد.
- ناهمواری و ظاهر نامناسب: میتواند ناشی از عدم پایداری قوس، سرعت نامناسب جوشکاری یا انتخاب الکترودی باشد که سرباره آن به سختی جدا میشود. انتخاب الکترود مناسب برای کیفیت جوش و کنترل صحیح پارامترها به بهبود ظاهر جوش کمک میکند.
نتیجهگیری
در دنیای جوشکاری که هر اتصال میتواند ضامن ایمنی یک سازه یا عملکرد یک قطعه حساس باشد، کیفیت جوش از اهمیت ویژهای برخوردار است. همانطور که در این مقاله بررسی شد، افزایش کیفیت جوش، فراتر از مهارت جوشکار و کارایی تجهیزات، به شناخت دقیق و انتخاب هوشمندانه بهترین الکترودها و مواد مصرفی جوشکاری گره خورده است.
از الکترودهای روپوشدار گرفته تا سیم جوشها و تنگستنها، هر کدام نقشی حیاتی در ایجاد خواص مکانیکی، پایداری قوس و ظاهر نهایی جوش ایفا میکنند. همچنین، گازهای محافظ و فلاکسها به عنوان مکملهای ضروری، حوضچه مذاب را از آلودگیها دور نگه داشته و به بهبود عملکرد کلی فرآیند کمک میکنند. یک رویکرد سیستماتیک در انتخاب این مواد، شامل شناخت فلز پایه، فرآیند جوشکاری، الزامات کیفی، شرایط محیطی و توجه به استانداردها، تضمینکننده دستیابی به جوشهایی با استحکام و دوام بالاست.
در نهایت، نمیتوان از اهمیت نگهداری صحیح مواد مصرفی چشمپوشی کرد. حفظ الکترودها و سیم جوشها از رطوبت و آلودگی، بازرسی منظم و توجه به توصیههای سازندگان، از بروز بسیاری از عیوب رایج جوش پیشگیری میکند. برای اطمینان از دستیابی به بالاترین استانداردهای کیفی در پروژههای خود، مشاوره با متخصصین و تهیه مواد مصرفی از تأمینکنندگان معتبر مانند آلیاژ صنعت ایلیا، گامی اساسی و هوشمندانه است. به یاد داشته باشید که سرمایهگذاری بر روی دانش و مواد مصرفی باکیفیت، در بلندمدت منجر به صرفهجویی در هزینهها، افزایش ایمنی و تضمین پایداری و دوام سازههای شما خواهد شد.
آیا شما به دنبال کسب اطلاعات بیشتر در مورد "افزایش کیفیت جوش با شناخت بهترین الکترودها و مواد مصرفی" هستید؟ با کلیک بر روی اقتصادی, کسب و کار ایرانی، اگر به دنبال مطالب جالب و آموزنده هستید، ممکن است در این موضوع، مطالب مفید دیگری هم وجود داشته باشد. برای کشف آن ها، به دنبال دسته بندی های مرتبط بگردید. همچنین، ممکن است در این دسته بندی، سریال ها، فیلم ها، کتاب ها و مقالات مفیدی نیز برای شما قرار داشته باشند. بنابراین، همین حالا برای کشف دنیای جذاب و گسترده ی محتواهای مرتبط با "افزایش کیفیت جوش با شناخت بهترین الکترودها و مواد مصرفی"، کلیک کنید.